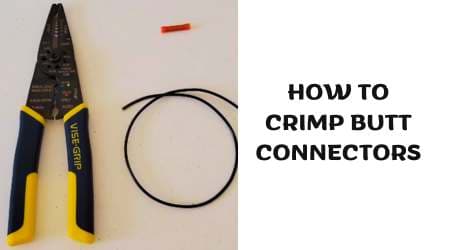
To crimp butt connectors, strip the ends of the wires and slide them into the connector. Use a crimping tool to securely fasten the connector to the wire.
Crimping butt connectors is an important skill for anyone who works with electrical wiring. These connectors are used to join two electrical wires together, allowing electricity to flow between them. When done correctly, crimped connections are reliable, durable, and safe.
It is important to choose the right size connector for your wire and to properly strip the ends of the wire before inserting them into the connector. In this article, we will guide you through the steps of crimping butt connectors and provide tips for achieving a secure connection.
Understanding Butt Connectors
If you are working on any electrical installation project, you might come across a small device called butt connectors. They might seem insignificant, but they play a crucial role in connecting wires together. Let's understand what butt connectors are, their types, why they're used, and their advantages and disadvantages.
What Are Butt Connectors?
Butt connectors are small metal or plastic tubes that provide a secure connection between two electrical wires. They are designed to connect two or more wires end-to-end without the need for soldering. Butt connectors come in a variety of sizes and materials, including copper, brass, and nylon.
Different Types Of Butt Connectors
There are two main types of butt connectors: crimp and non-crimp. Crimp connectors involve compressing the wire with a crimping tool to secure the wire into place. Non-crimp connectors utilize a set-screw mechanism to hold the wire in place.
Below are the different types of butt connectors:
- Standard butt connectors: They are the most commonly used connectors, made of copper with a protective coating of nylon.
- Bullet connectors: These are small connectors made of brass, which are rounded on one end with a tube on the other end.
- Heat-shrink butt connectors: These have a heat-activated adhesive that creates a waterproof seal when heated, useful for outdoor wiring projects.
- Closed end connectors: They have a plastic sleeve at one end and small internal metal teeth that grip the wires.
- Parallel connectors: They are perfect for splicing two wires of the same diameter, side-by-side.
Why Use Butt Connectors?
Butt connectors provide a secure and strong electrical connection between wires. They are easy to use and cost-effective. Other benefits of using butt connectors include:
- They are vibration-resistant and can handle high voltage and current.
- Create a waterproof seal, making them ideal for outdoor splice applications.
- They provide a more professional-looking finish than just using electrical tape.
- Butt connectors eliminate the need for soldering, which can be difficult and time-consuming.
Advantages And Disadvantages Of Butt Connectors
Like any other electrical component, butt connectors have their advantages and disadvantages:
Advantages:
- Easy to use and install
- Available in a variety of types and sizes
- Cost-effective
- Provide a strong and secure connection
Disadvantages:
- If not crimped properly, the connection could become loose over time.
- Over-crimping the connector can damage the wire.
- Some butt connectors tend to corrode over time, causing damage to the wire.
Butt connectors are important components for connecting electrical wires correctly. You should choose the appropriate butt connector based on your project requirements to achieve a secure and reliable connection.
Tools And Equipment Needed
Essential Tools And Equipment For Crimping Butt Connectors
Crimping butt connectors is a vital skill for anyone working with electrical wiring. You can't get it right without the correct tools and equipment. Here are the essential tools and equipment you'll need:
- Wire strippers: A tool used to strip the protective coating off electrical wires.
- Crimping tool: A plier-like tool used to crimp the connector onto the wire.
- Butt connectors: A cylindrical tube-like connector that joins two wires together.
- Heat gun: Used to shrink heat-shrink tubing to seal the connector.
Tips For Selecting Quality Tools
Choosing the right tools and equipment is essential to ensure a reliable and safe electrical connection. Here are some tips to help you select quality tools:
- Go for trusted brands: Brands known for producing quality tools are typically more reliable than lesser-known brands.
- Material: Look for tools manufactured from high-quality materials that can withstand frequent use without breaking or bending.
- Ergonomic design: Tools designed with ergonomics in mind are more comfortable to use, resulting in more precise crimping.
- Size compatibility: Check the size of the crimping tool before purchasing to make sure it is compatible with the connectors you plan to use.
Remember, using quality crimping tools and equipment is key to getting the job done right the first time. Don't compromise on quality!
Preparing To Crimp Butt Connectors
Assessing The Wires That Need To Be Connected
Before crimping butt connectors, the first step is to assess the wires that need to be connected. Here is everything you need to know to conduct a thorough assessment before crimping:
- Check the wire gauge: Make sure to choose a connector that matches the wire gauge. The connectors will have a range of wire gauges that it can accommodate. Ensure the wire gauge matches the connector.
- Inspect the insulation: Wires with damaged insulation can cause electrical issues. Inspect the insulation of all wires to ensure they're in good condition.
- Determine the wire type: Identify the type of wire that needs to be connected to determine the appropriate connector to be used.
- Check the length of wires: Measure the wires and ensure that the length is enough to fit the crimp connector properly.
Stripping And Preparing Wires For Crimping
Stripping the wires is an important process when preparing wires for crimping butt connectors. A poorly stripped wire can cause issues with the crimping process. Here are some points to follow to ensure the wire preparation process goes smoothly:
- Use a wire stripper tool: A wire stripper is the best tool to use when stripping wires. Make sure to select the correct tool size and use it to cut the insulation off the wire.
- Strip at the correct length: Strip the insulation of wire to the length needed for the connector. Use the gauge markings on the wire stripper as a reference.
- Remove any frayed wires: Use small pliers to remove any frayed wires or stranded wires sticking out of the insulated wire.
- Twist the wire strands: Once you've stripped the wire, twist the wire strands together tightly to prevent them from separating during the crimping process.
Choosing The Correct Butt Connector
Choosing the correct butt connector is the final step in preparing for crimping. Here is how to select the appropriate connector:
- Determine the wire gauge: The wire gauge dictates the connector size that needs to be used. Choose a connector that can accommodate the wire gauge size
- Choose the connector type: There are various types of butt connectors available and each one is designed for specific applications. Select the appropriate connector based on the type of wire and the application.
- Inspect the connector: Check for any defects or issues with the connector before crimping the wires.
- Place the connectors correctly: Ensure the crimper and connectors are orientated correctly before you start and insert the stripped end of the wire into the butt connector, being careful not to twist the wires together.
Step-By-Step Guide To Crimping Butt Connectors
Learning how to properly crimp butt connectors is an essential skill for those who work with electrical wiring. Whether you are a beginner or an experienced electrician, a secure and reliable connection is crucial to ensure your safety and the longevity of your wiring projects.
Below is a step-by-step guide on how to crimp butt connectors.
Inserting The Wire Into The Connector
- Start by selecting the appropriate size of butt connector that matches your wire gauge.
- Strip the wire insulation to the length specified by the particular connector that you are using.
- Insert the stripped wire into the connector barrel, making sure that the wire is flush with the connector's end.
- Use pliers to crimp the connector barrel firmly around the wire insulation.
Using Crimping Tools To Make A Secure Connection
- Select the correct crimping tool for your connector type.
- Position the connector in the proper crimping slot or cavity based on the connector model.
- Squeeze the tool handles tightly together to make a secure crimp around the wire and connector barrel.
- Visualize the crimp to ensure that the wire is secured and attached correctly to the connector.
Inspecting The Connection For Security
- Check the connection visually by making sure that the wire is securely attached to the connector barrel and that there is no protruding wire or connector pieces.
- Use a tug test to ensure that the wire does not easily pull out of the connector barrel.
- Check for any sign of overheating or burn marks on the connector barrel or wire insulation, which may indicate a loose connection or incorrect crimping process.
Tips For Crimping Multiple Wires Together
- Use multi-wire butt connectors that can accommodate the number of wires you will be crimping together.
- Strip the wire insulation to the required length and twist the wires together before inserting them into the connector.
- Arrange the wires evenly around the connector barrel, ensuring that each wire is in the crimping slot or cavity.
- Use the correct crimping tool based on the connector type and number of wires you are crimping together.
Common Mistakes To Avoid During The Crimping Process
- Do not use the wrong size of butt connector for your wire gauge as it can weaken the connection and pose a safety hazard.
- Do not strip too much or too little insulation from the wire, as this can result in loose connections or damage to the wire.
- Avoid over-crimping or under-crimping the connector barrel around the wire as it can result in loose connections or damage to the wire.
- Avoid using inferior quality connectors or tools as these can lead to poor quality connections and potential hazards.
By following these step-by-step guidelines on how to crimp butt connectors and avoiding common mistakes, you can create secure and reliable connections in your electrical wiring projects.
Read Also: Can You Split Ethernet Port
Testing And Inspecting Crimped Butt Connectors
Crimping butt connectors is an essential electrical task that requires precision and attention to detail. Understanding how to crimp connectors and do it correctly can ensure that your electrical connections are safe, secure, and reliable. In this section, we'll delve into the critical aspect of testing and inspecting crimped butt connectors, which can save you from electrical hazards down the line.
How To Test The Conductivity And Strength Of A Crimped Connection
To ensure that your crimped butt connectors are conducting electricity efficiently and have the strength and durability to last long, testing the crimped connection should be the next step. Here's how to do it:
- Get yourself a multi-meter and set it to measure resistance. Place one end of the multi-meter on one end of the crimped connector and the other on the other end. The readings should indicate no resistance, and if there is, you might have a poor connection yet to be addressed.
- To determine the strength of the crimp, grip the wire firmly and tug on it gently. If it can withstand pulling and twisting without fraying or disconnecting, then the connection is sound.
Inspecting The Crimped Connection For Flaws
Once you've done the strength test, inspecting the connector for imperfections is the next step. Here are some of the issues you need to be on the lookout for:
- The insulation sleeve, which covers the connection, should be in place and can withstand any pull or tug without fraying or tearing.
- The crimp barrel should not be distorted, and the wire should be centered within the connector. If the wire is not correctly aligned within the barrel, it could lead to connectivity problems or a high resistance connection.
- The crimp barrel should come into full contact with the wire without hurting or flattening it in the process.
Troubleshooting Common Issues With Crimped Connections
Even after a successful crimping process, common problems can emerge, so it is crucial to troubleshoot and identify them early to avoid electrical hazards. Here are some of the common issues with crimped butt connectors:
- Insufficient tension: This issue arises when the crimper doesn't apply enough force or pressure to crimp the wire correctly. The solution is to redo the crimping process and make sure the tool applies the require pressure.
- Over-crimping: Applying too much force or pressure when crimping the connector can cause the connector to split or deform, leaving behind bulges that weaken the connection. The solution is to redo the crimp and apply moderate force.
- Incorrect wire size: Using a connector that is too small or too large for the wire size can cause the wire to disconnect from the connector, resulting in an electrical hazard. The solution is to use connectors that match your wire size.
Testing and inspecting crimped butt connectors is crucial to ensure efficient electrical conductivity, durability, and safety. By following the above guidelines, you can make sure your crimped connections are of high quality and error-free.
Frequently Asked Questions For How To Crimp Butt Connectors
How Do You Crimp A Butt Connector?
To crimp a butt connector, strip the wire, insert the stripped wire into the connector, and then use crimping pliers to squeeze the crimps. Make sure that the wire is secured in the connector and the crimps are tight and secure.
What Type Of Wire Should Be Used With Butt Connectors?
Butt connectors are designed to be used with stranded wire. They are not recommended for use with solid-core wire. Stranded wires are more flexible and can be easier to work with when using butt connectors.
Can You Reuse A Crimped Butt Connector?
It is not recommended to reuse a crimped butt connector as the crimp may not be secure enough to hold the wire properly. It is best to use a new butt connector each time you need to make a connection.
What Is The Difference Between Insulated And Non-Insulated Butt Connectors?
Insulated butt connectors have a plastic cover that provides extra protection against moisture and corrosion. Non-insulated butt connectors do not have this cover and are more suitable for dry and less demanding applications.
How Do You Select The Right Size Of Butt Connector?
Selecting the correct size of butt connector is essential for a secure connection. The size of the butt connector is based on the wire gauge. Be sure to choose the correct gauge size for your wire, and ensure that the connector is rated for the current and voltage of your application.
What Are The Benefits Of Using Butt Connectors?
Butt connectors provide a quick, reliable, and secure way to join wires. They are easy to use, and they can help simplify the wiring process. With different types of butt connectors available, they can be used in a variety of applications, such as automotive, marine, and industrial.
Conclusion
Crimping butt connectors is an essential skill for any diy electrician or technician. By following the steps outlined in this blog post, you can successfully complete the process and ensure a safe and secure electrical connection. Always use the proper tools and materials, double check your work, and test your connections before finalizing your project.
Remember to choose the right size and type of butt connector for your job, as well as the correct crimping tool. With these tips in mind, you can confidently tackle any project that requires crimping butt connectors. So start practicing and perfecting your technique, and you’ll be a pro in no time!